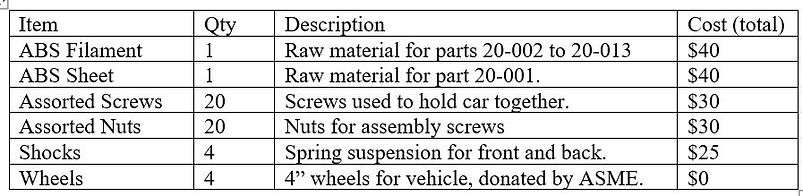
Budget
Nearly all of the parts were made from ABS using a 3D printer or acrylic using a laser cutter. The few parts not manufactured were ordered from Amazon (shocks), donated by ASME (wheels), or were fasteners purchased at Ace Hardware. The chassis plate was the most expensive part. In order to reduce costs, all custom parts were manufactured locally.
The project is significantly under budget mostly because the wheels, which would have been the most expensive part of the project, were donated by the ASME club. Only half of the project budget was used. Because the 3d printed parts all came from a roll of filament bought for the project, additional prints due to error did not increase the cost of the project. All of the purchased parts were either bought in person or from Amazon with Prime so there were no additional shipping costs.
Had the wheels not been donated by the ASME club, they would have been the most expensive parts on the car, so not needing to buy these drastically reduced the cost of the project. The shocks were less expensive than the roll of filament for the 3d printed parts, but at about $5.50 per shock, they are a major contributor to the cost of the project. However, the material for the chassis was the most expensive part. Nuts and bolts are the smallest contributor to the budget at less than $10 combined.
Most purchases went smoothly like the sheet plastic for the chassis plate, which the team had by the end of the second week of class, which lines up well with the proposed timeline (order in January). The shocks had also arrived on time (within the first two weeks of class) but had to be returned and repurchased because the original set were bent. This caused a slight delay, but measurements were taken from the bent set to redesign parts like the shock tower and the replacement parts had arrived by the time the reprints were finished.

Schedule
The basic design process of the project was finished before winter break (November 20, 2020), including the first iteration of the complete project report. The budget and project were both determined during week one. Part drawings were be completed between weeks five and ten. The introduction, design and analysis sections of the report were be done by week six. The first analysis to be done was the chassis plate, followed by the front bumper, and suspension related analyses. The suspension of the car has many components so every nearly every analysis from week three to ten was related to the suspension as seen in the Gantt chart. The discussion and conclusion were written in week ten. The first full version of the report, which contained all information relating to the design portion, was due Tuesday of finals week (November 17, 2020).Finally, parts were ordered starting in week eleven.
To avoid a time crunch in the final weeks of the project, as much manufacturing as possible was done within the first four weeks. Any parts not purchased were 3d printed except for the chassis plate due to size constraints. This made the manufacturing process relatively quick and hands off so redesigns could be performed in SolidWorks while other parts were manufactured. Initial prints of the 3d printed parts were completed by week three and the next five weeks were focused on redesigning parts based on available fasteners and unforeseen problems like too much flexing in the steering assembly. The early push to finish everything except the chassis plate helped to prevent issues when installing the steering components by allowing time for small reconfigurations of the steering system after the chassis and suspension were completed.
The testing period was busiest at the beginning as all testing was completed by the end of the fifth week of spring quarter. This included testing as well as any repairs that were needed. The biggest issue was ensuring everything was finished in time for SOURCE.